What is CAN bus and how does it work?
A Controller Area Network (CAN bus) is a powerful vehicle bus standard that enables communication between microcontrollers and electronic control units (ECUs). It’s a message-based protocol that can be used in many ways but was originally designed for multiplex electrical wiring within vehicles. It was introduced with the main purpose to save on copper.
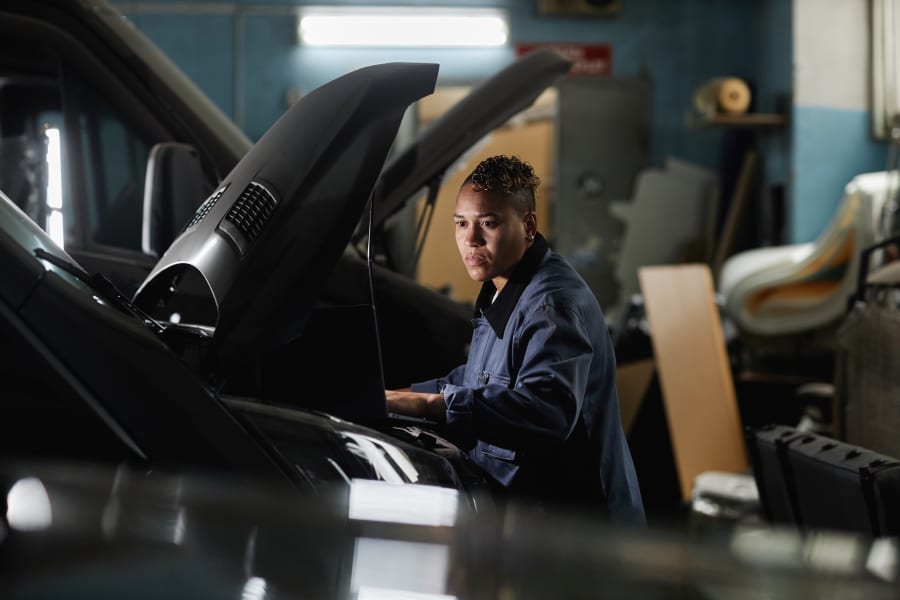
CAN bus explained
CAN bus can be described as acting like a central nervous system for a vehicle. All ECUs are interconnected via the CAN bus system. Much like the human body, information from one part can be shared with another. And the part receiving the information will determine whether to accept it or ignore it. In other words, whether it’s relevant or not to that specific part.
iCompario tip:
Initially developed by Bosch, CAN bus can be used with telematics to give accurate vehicle information. A fleet manager can then see all the CAN bus data on a screen to get remote vehicle diagnostics.
What’s an ECU?
Part of a vehicle’s CAN bus system, electronic control units (ECUs) are small devices that control specific functions. For example, the engine control unit, power steering control, airbags, power windows, seats, audio system, etc.
There can be up to 100 ECUs in modern vehicles and each hold information that is relevant to other parts of the network. For that reason, it’s important to ensure communication across the network and that’s exactly what the CAN bus does.
How does CAN bus work?
The CAN bus system makes the communication between all ECUs possible without complex wiring. Because ECUs cannot send data directly to each other.
Instead, they use the CAN network. An ECU transmits data via the CAN bus and the data is accepted by all ECUs part of the CAN network. From here, each ECU checks the data and decides whether it’s relevant or not.
The data is sent in frames and there are four different frames with CAN:
- Data frame – a frame to transfer data to other ECUs
- Remote frame – a frame to request data from other ECUs
- Error frame – just like the name suggests, a frame that detects and reports errors
- Overload frame – a frame to report any overload conditions
CAN bus applications
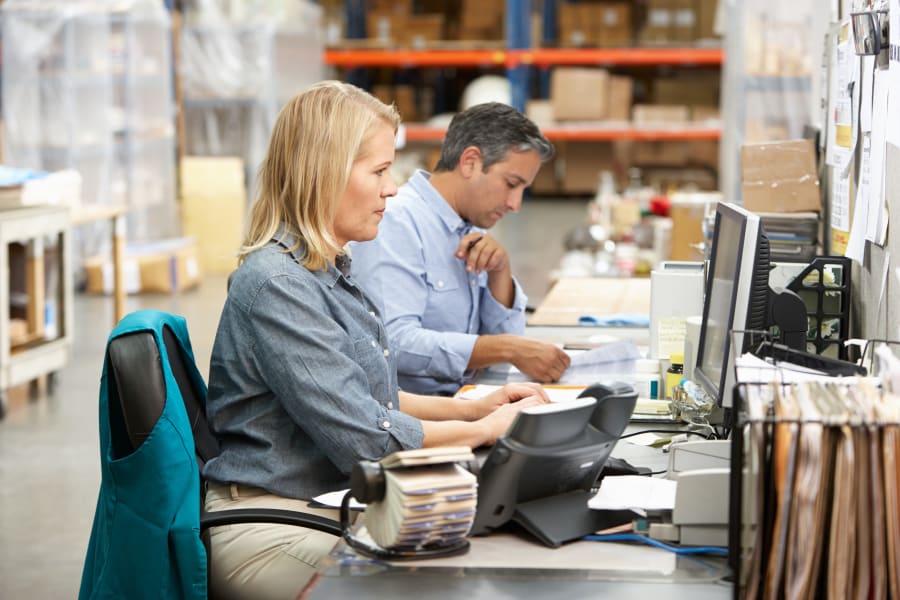
A Controller Area Network has multiple applications, but the main one is in the automotive industry. And that’s what we cover in this guide.
One major advantage of CAN bus in vehicles is that by connecting systems inside, it lets you use a bunch of safety, economy and convenience features using software alone. That would be too costly and complex if traditional automotive electrics were to be used.
Let’s take a few examples:
- Manufacturers can add sensors in convenient places on a vehicle. ECUs can use the data from these sensors. Like outdoor temperature sensors can be placed in the mirrors and data from these sensors can be used by the climate control system, the driver display, and even the engine.
- Sensors from the seat belts transmit data to the CAN bus to determine whether the seat belts are fastened.
- Parking assist systems. When the driver puts the car in reverse gear, the CAN bus receives data from the transmission control unit, which is used to activate parking sensors.
- The CAN bus also takes inputs from the rain sensor to trigger the windscreen wipers.
Benefits of CAN bus
The CAN bus system brings key benefits such as:
1. Simplicity
The CAN bus eliminates the need for complicated hard wiring. ECUs are able to communicate directly through a single CAN bus system. That reduces errors, costs and helps manufacturers to design lighter vehicles.
2. Efficiency
Because ECUs can communicate so easily through CAN bus, no data is lost and crucial data gets immediately at the right ECU. That means less errors, less interruptions and a better view of the vehicles systems.
3. Centralisation
The CAN bus means one network for all the ECUs to communicate with each other. That enables central diagnostics, configuration and data logging.
4. Reliability
The CAN bus is a robust and reliable system safe from electromagnetic interferences and electric disturbances.
CAN bus and telematics
CAN data can be tapped by telematics systems to transmit all the information to a software platform remotely. That means that you can then see all the CAN bus data on a screen to get remote vehicle diagnostics.
There are two ways in which a telematics system can gather data. One is through the data through the on-board diagnostics port (OBD-11), while the other is through CAN bus. The data gathered through the CAN bus is usually more reliable.
Based on this data, the telematics system will put together certain reports that can give important business insights.
The data captured can include:
- Vehicle location. Precise location data so you’ll always know where your vehicles are.
- Geofencing. Read about geofencing in our guide.
- Vehicle speed, acceleration, harsh braking and cornering.
- Vehicle diagnostics. Make sure all vehicle maintenance is done on time. Avoid unpleasant break-down and costly repairs.
- Tachograph data. With digital tachographs you can check remotely that your drivers comply with driver’s hours regulations.
- Temperature monitoring. Sensitive cargo that needs to have a constant temperature? Now you can keep an eye on it all the time.
- Fuel volume. Check if your vehicles need filling up before a job.
- Odometer. Use this data to keep up with vehicle maintenance.
How can telematics help your business?
Telematics is a great solution for businesses of all sizes and types. You can use it to monitor one vehicle or an entire fleet.
All the data gathered by telematics through the CAN bus can be instrumental in boosting your business’ productivity.
You can use it to improve your customer service. Based on your vehicle tracking data, you can provide your customers with accurate ETAs, or you can decide faster which vehicle to dispatch to a certain job.
You can lower your fuel and maintenance costs. You get detailed vehicle diagnostics. You get driver behaviour reports. All together can ultimately help you to save you a lot on fuel and maintenance in the long run.
You ease your admin work by a lot. You get digital tachograph data, so you eliminate the need to bring the vehicles in to check the tachograph. You get automated mileage expense reports that will greatly simplify admin and compliance.